Why are there part lists for ships but not for houses?
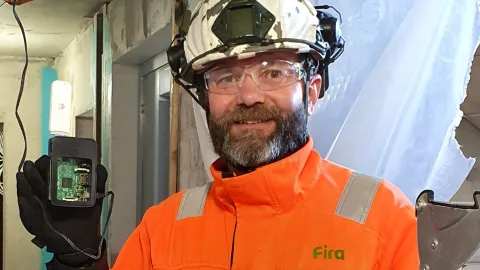
– The lead times on construction sites are terribly long. If the manufacturing process of a construction part takes a total of 80 hours, its implementation takes 12–14 weeks in practice at the construction site. For work productivity to increase, construction industry professionals must be able to focus on their actual work and its flow to shorten turnaround times, states Otto Alhava, CTO of Flow Technologies and vice-chairman of the Digitalization group of the Confederation of Finnish Construction Industries RT. In the Road map subgroup under the Digitalization group, Alhava works for the implementation of GS1 standards.
Alhava states that the use of standards in the construction product industry is already in good shape, especially in electro-technical and HVAC supply chains. However, more could be done in the management of supply chains – the chains connect factories of the construction product industry to the construction sites.
– If all products had GTINs and identified storage locations on construction sites, we could bring to construction sites the internal logistics familiar from factories. All used material could be read digitally, which would enable precise deliveries of products to storage and installation locations on the construction site. In this way, we would also have an accurate list of the installed parts. Why does the manufacturing process of ships produce parts lists, but not the manufacturing process of houses?, asks Alhava.
Effective procurement begins in the planning phase
Alhava states that with the introduction of standards, construction would become more efficient from the moment of purchase, since already at the planning level the used products could be named with purchase titles. The plans could be made into workshop-level pictures, showing all the necessary parts. In this case, the selection of suitable parts would not be left to the subcontractor's employee at the site, and the construction professional would not need to be there to receive and inspect the goods arriving at the site either. This work could be handled by logistics professionals.
– With the widespread adoption of standards, all product information and logistics information could be digitalized. Currently, ordering goods requires manual work from both the orderer and the recipient. The identification of products opens the possibility for us to automate data processing for all parties, which benefits everyone in the industry, explains Alhava.
All information needs to be captured
In addition to making work more efficient, common standards would also improve the quality management of buildings and serve the occupational safety of construction sites. When the used elements and products have their own identifiers, information such as weight or standard defects can be automatically added to them.
– The code that works electronically can be read with a suitable application, even on a phone - since we all already have a barcode reader in our pocket. It allows us to both receive and enter information about the products used in the building into a common database that all parties can use. The management of the material flow from the factory to the building could already be made to produce readiness level information for both the builder and the customer with the current barcodes. With the help of the same identifiers, we could pass on the product information to the user and administrator of the building. Now we lose information all the time because we don't have the ability to machine read it into the cloud at the construction site, Alhava explains.
Product identification improves the life cycle management of buildings when information about the use of building materials creates the basis for building maintenance. When it is clear how many pieces of which product are in which place, and who installed them under what conditions, maintenance and renovation of the building becomes easier. The unique code can be used to find out what the damaged material needs to be repaired or replaced with. Accurate information about the products used also enables the automation of the calculation of the building's carbon footprint.
Cooperation has clear benefits below the line
The locality of the business and varying production methods are the reasons why the introduction of standards in the construction industry has been slow. According to Alhava, the efficiency enabled by the standards can only be achieved through cooperation across the boundaries of companies and projects. This work is already being done in Norway, Denmark, and Sweden.
– It all starts with the industry deciding together to fix this thing, supply chain by supply chain. We can follow the example of our neighboring countries. The construction industry needs to organize itself around supply chain types. These parts would already have nationally capable and functioning organizations in place. We can also take a model from HVAC and electrical industry logs; they have already solved product individualization and transport identification for their products and use GTIN and SSCC standards in their daily business. We need an agile national umbrella organization to guide different committees, each of which is responsible for one supply chain. The group responsible for implementing the GTIN standard with concrete elements does not have to wait for the decision to use the GTIN for kitchens, but the working groups can proceed at their own pace. Even with a very small group, you can achieve the standard of your own supply chain, explains Alhava.
Apart from organization, the introduction of standards also requires software and barcode readers that work for identification codes. There are several solution providers and alternatives, and deciding on the application method of the standards would open up the construction industry to the software industry operating in other industrial sectors. Investments in ready-made solutions pay off and bring clear savings to all players in the industry.
– For individual operators, the benefit comes specifically below the line. Using standards creates traceability, situational awareness, and the possibility of automation. The machine checks the work steps, and they are not left depending on the attention of individual people. This is like using a navigator in a car – the machine takes care of navigation, and the person behind the wheel can focus on safe driving, Alhava compares.